Electroplaters need cells like bricklayers need trowels
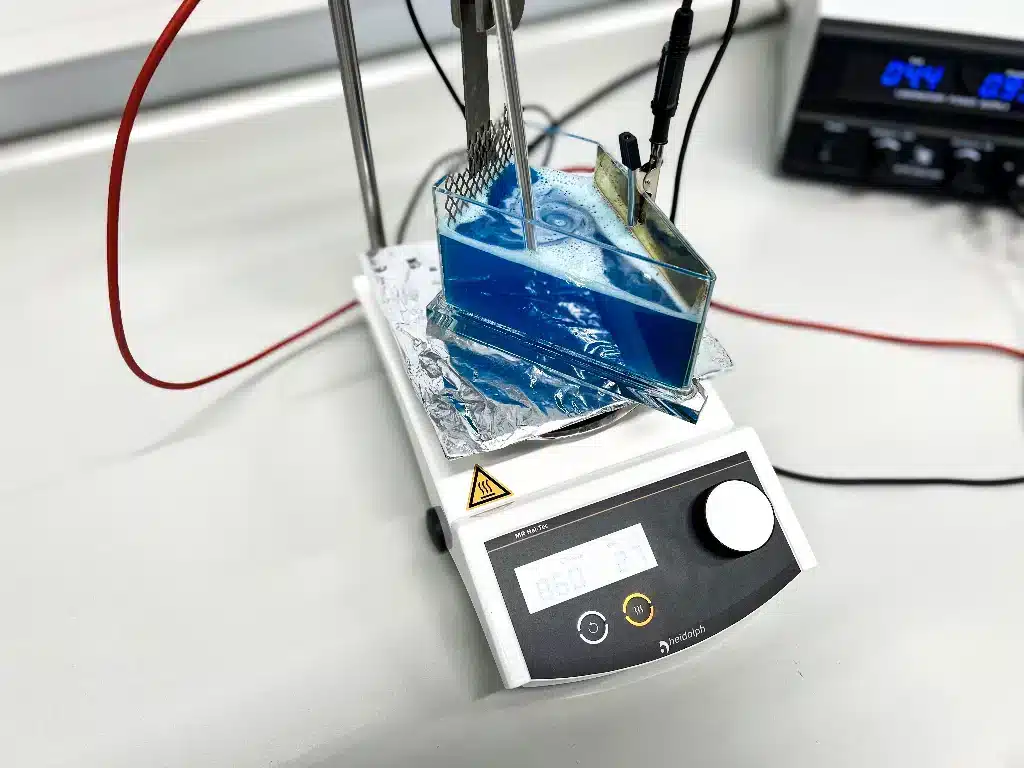
Electroplaters need Hull cells just like doctors need stethoscopes and bricklayers need trowels: these cells are simple, but extraordinary versatile tools that aid in the development and testing of electroplating processes and have proved their worth over many years. The Hull cell helps in evaluating the deposit, even in cases close to current density limits, and makes it possible to assess electrolyte composition with the right type of experience.
A seminal invention by R.O. Hull
The cell named after its American inventor R.O. Hull is basically a standardized electroplating bath shrunk to laboratory dimensions. Hull developed this small, transportable electrolysis unit to check electrolytic baths quickly and simply under almost real-life conditions in the 1930s. The cell consists of a trapezoidal container made of insulated material, mostly PVC, which holds either 250 or 1,000 ml and electrodes that are arranged so that the anodic and cathodic effects can be observed across a wide range of current densities. IWG, like many other laboratories, uses the smaller Hull cells as they are easier to work with.
Results after only one attempt
Hull cells allow process testing for an entire current density range in one go, instead of testing electro-chemical deposition processes at one specific current density after another. The reason for this is the trapezoidal shape of the Hull cell, in which the anode and cathode are not arranged in parallel, but at angles to each other. The different distances to the anode results in the current varying along the cathode, ending in deposition with increasing current density. However, the current density distribution is not linear, but increases faster as the distance decreases. The anode material is chosen in accordance with the electrolytes to be tested (e.g. pure copper for copper electrolytes). The cathode, on the other hand, is a brass test panel.
Its versatility has made the Hull cell a vital part of electroplating. Hull cell testing can be especially effective when integrated optimally into the different methods used in the plating process. At IWG, we not only use Hull cells in the development of new electrolytes, but also when assessing the impact of individual electrolytic components or checking layer properties, such metal distribution, gloss, roughness, layer thickness and alloy composition.
Reliable results thanks to staff know-how
The effects of bath parameters — such as temperature, pH value, the composition of electrolytes, and potential contamination — on the properties of the layer deposited can be determined using Hull cells, but still require many years of experience and know-how to yield reliable results. After all, the assessment is based on visual appearance: is the test panel glossy, matte, rough, spotty, or porous? Physical layer properties, such as adhesive strength or ductility are evaluated by our lab technicians using a bending test. Layer thickness and distribution is measured across the entire panel using X-ray fluorescence, aiding the evaluation of the throwing power of a bath.
Many of our electrolytes need working temperatures that are higher than room level. This is why we use heating plates with integrated magnetic stirrers, which also provide the right level of electrolyte movement.