Zinc-Nickel coatings from IWG
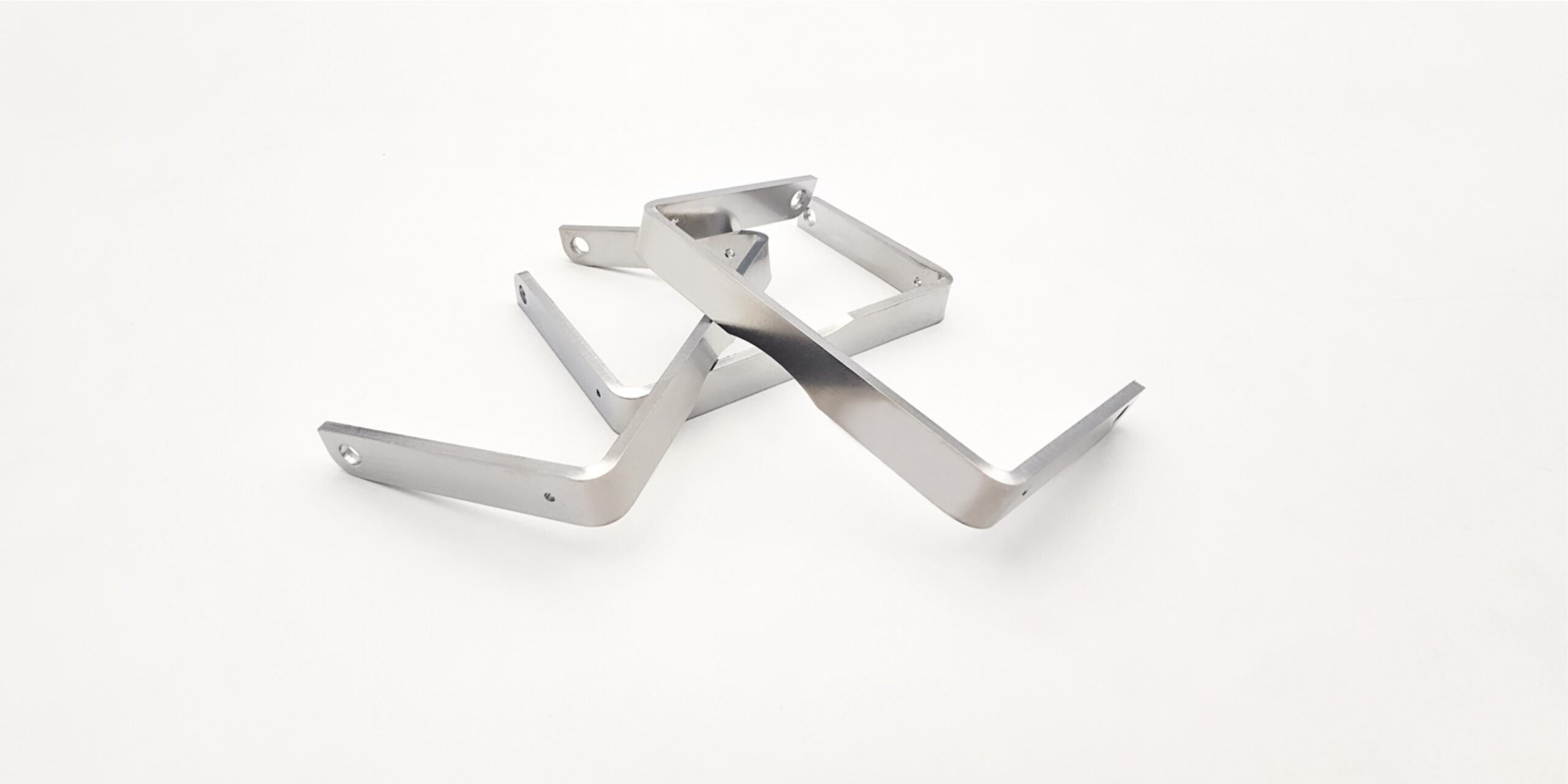
Premium corrosion protection – not only – for automotive industry
The zinc-nickel coating process is the solution for anyone with the highest demands on corrosion protection. This high-performance coating has proven itself in the automotive, aviation and electrical industries in particular thanks to its outstanding resistance and durability.
Why zinc-nickel coatings?
- ✅ Superior corrosion protection: Thanks to an innovative alloy of 85-87% zinc and 13-15% nickel, the coating reliably protects your steel components against rust and wear – even under extreme conditions. The zinc-nickel coating offers far better corrosion protection than pure zinc coatings, especially in environments that are exposed to highly corrosive conditions such as moisture or road salt, for example. This is crucial for the longevity of vehicle parts that have to function under extreme conditions. In addition, zinc-nickel from IWG is easy to passivate.
- ✅ Endurance and durability: Components in vehicles, such as brake lines, chassis components and screws, are constantly exposed to mechanical stress and temperature fluctuations. The zinc-nickel coating not only offers protection, but also withstands these mechanical stresses, and IWG’s zinc-nickel has good passivation properties.
- ✅ Sacrificial anode effect with delayed passivation: Zinc acts as a “sacrificial anode” and protects the underlying metal (usually steel) by preferentially corroding it. The nickel content in the alloy ensures that the passivation of the zinc is delayed, which maintains the protection in the long term.
- ✅ Temperature resistance: Zinc-nickel coatings are more heat resistant than pure zinc coatings, making them particularly suitable for applications where parts are exposed to high temperatures (such as in engine compartment environments).
Highest quality standards at IWG
The specific composition of the zinc-nickel alloy offers an optimal combination of corrosion protection, mechanical resistance and temperature resistance, making the process the preferred choice in many industrial applications. However, careful process control is required during implementation, and we will be happy to assist you with this.
Process sequence for coating with zinc-nickel:
- Pre-treatment: Degreasing, pickling and activation of the surface.
- Coating: Deposition of the zinc-nickel layer in an electroplating bath at 20-30°C and a current density of 2-5 A/dm².
After pre-treatment, the actual electrolytic deposition takes place in a bath, which is typically operated at temperatures of 20-30°C. A constant current density of around 2-5 A/dm² is applied to ensure uniform layer deposition.
During the coating process, the workpiece is used as a cathode and an insoluble anode. The metal ions from the solution migrate to the cathode under the influence of the electric field and form the zinc-nickel layer there.
The typical composition of the zinc-nickel coating consists of 85-92% zinc and 8-15% nickel. This specific composition ensures an optimum combination of corrosion protection and mechanical resistance.
Areas of application for zinc-nickel:
Zinc-nickel coatings are used in many industrial sectors, including:
- Automotive industry: Protection of vehicle components such as brake lines, screws and chassis components that are exposed to highly corrosive conditions.
- Aerospace: Application on components that are exposed to extreme environmental conditions and high mechanical loads.
- Electronics industry: Protection against corrosion to ensure reliable function.